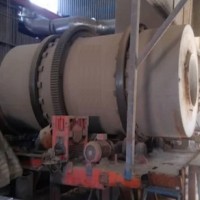
what are Rotary furnaces
Rotary furnaces
Rotary melting furnaces, also known as melting furnaces, are advanced industrial equipment used for the melting and processing of various materials. These furnaces are designed with a rotating drum that allows for efficient and uniform heat distribution, ensuring a thorough melting process. melting furnaces are widely used in industries such as metal casting, glass production, and chemical processing. They offer numerous advantages, including increased productivity, energy efficiency, and flexibility in handling different materials. In this article, we will explore the features, benefits, and applications of melting furnaces, highlighting their crucial role in modern manufacturing processes.
1. The Advantages of Rotary Melting Furnaces
Rotary melting furnaces are a type of furnace that offer several advantages in the melting process. These furnaces are designed with a rotating drum, which helps to efficiently melt various materials. One of the key advantages of rotary melting furnaces is their high melting capacity. Due to the rotating drum, these furnaces can accommodate a large volume of materials, allowing for a higher production rate.
Additionally, rotary melting furnaces offer excellent temperature control. The rotation of the drum ensures a more uniform distribution of heat, resulting in a consistent melting process. This temperature control is crucial in industries where precise melting temperatures are required for the desired outcome.
Another advantage of rotary melting furnaces is their versatility. These furnaces can handle a wide range of materials, including metals, alloys, and other substances. This versatility makes them suitable for various industries, such as foundries, metalworking, and recycling. Whether melting scrap metal or producing new alloys, rotary melting furnaces can effectively handle different materials.
In terms of energy efficiency, rotary melting furnaces are also advantageous. The design of these furnaces minimizes heat loss, ensuring that the majority of energy is used for the melting process. This energy efficiency not only reduces operating costs but also contributes to a more sustainable and environmentally friendly approach to melting.
Furthermore, rotary melting furnaces offer a safer working environment. The rotating drum helps to prevent the formation of hot spots, reducing the risk of accidents or damage to the furnace. This safety feature is essential for industries where employee well-being and equipment protection are top priorities.
In conclusion, rotary melting furnaces provide several advantages in the melting process. Their high melting capacity, temperature control, versatility, energy efficiency, and safety features make them a valuable asset in various industries. Whether it is for melting metals, alloys, or other materials, these furnaces offer a reliable and efficient solution.
2. Innovations in Modern Rotary Melting Furnaces
Innovations in modern rotary melting furnaces have revolutionized the metal casting industry by improving efficiency and reducing energy consumption. These furnaces utilize advanced technology to melt various types of metals, such as aluminum, copper, and iron.
One key innovation in modern rotary melting furnaces is the use of advanced refractory materials. These materials have high resistance to heat and can withstand the extreme temperatures required for melting metals. This not only increases the lifespan of the furnace but also ensures consistent and efficient melting processes.
Another innovation is the incorporation of automated controls and monitoring systems. These systems allow for precise control of temperature, airflow, and fuel consumption, resulting in optimized melting conditions. The real-time monitoring of various parameters ensures that the furnace operates at its optimal performance, reducing energy waste and improving productivity.
Furthermore, modern rotary melting furnaces are equipped with advanced combustion systems. These systems use efficient burners and combustion chambers to maximize heat transfer and minimize heat loss. This results in reduced fuel consumption and lower greenhouse gas emissions, making the furnaces more environmentally friendly.
Additionally, modern rotary melting furnaces are designed with improved safety features. These include advanced insulation materials to prevent heat loss and minimize the risk of accidents. The furnaces also have automated shut-off systems that activate in case of any abnormalities, ensuring the safety of operators and preventing damage to the furnace.
In conclusion, innovations in modern rotary melting furnaces have significantly enhanced the metal casting industry. These advancements in refractory materials, automated controls, combustion systems, and safety features have led to increased efficiency, reduced energy consumption, and improved productivity. The utilization of these technological advancements has paved the way for a more sustainable and cost-effective metal melting process.
3. Enhancing Efficiency in Melting Processes with Rotary Furnaces
Rotary furnaces are a crucial component in the melting processes of various industries. These furnaces play a significant role in enhancing efficiency and productivity in the melting processes. They are designed to provide a controlled and consistent heat source for melting different types of materials.
One of the key advantages of rotary furnaces is their ability to melt materials at a faster rate compared to other types of furnaces. The rotating motion of the furnace ensures a uniform distribution of heat, which leads to a quicker melting process. This increased efficiency can significantly reduce the overall production time and costs.
Furthermore, rotary furnaces are highly flexible and adaptable to different types of materials. They can accommodate a wide range of materials, including metals, alloys, and various industrial waste products. This versatility makes rotary furnaces a valuable asset for industries that deal with a diverse range of materials.
In addition to their efficiency and adaptability, rotary furnaces also offer improved energy efficiency. These furnaces are designed to minimize heat loss, ensuring that the maximum amount of heat is utilized for the melting process. This not only saves energy but also reduces operational costs for industries.
Another notable advantage of rotary furnaces is their compact size and space-saving design. These furnaces can be installed in smaller spaces, making them suitable for industries with limited floor space. The compact design also allows for easy integration into existing production lines, minimizing disruptions to the workflow.
In conclusion, rotary furnaces play a vital role in enhancing efficiency in melting processes. They offer faster melting rates, flexibility in accommodating various materials, improved energy efficiency, and space-saving design. These advantages make rotary furnaces a valuable asset for industries looking to optimize their melting processes and improve overall productivity.
4. Exploring the Versatility of Rotary Melting Furnaces
Rotary melting furnaces are versatile equipment used in various industries for the melting and processing of different materials. These furnaces are designed to handle a wide range of materials, including metals, alloys, and other substances.
One of the key advantages of rotary melting furnaces is their ability to accommodate different types of material. They can handle both solid and liquid materials, allowing for flexibility in the melting process. This versatility makes them suitable for a variety of applications, ranging from metal casting and recycling to the production of specialty alloys.
Another benefit of rotary melting furnaces is their efficient heat transfer capabilities. The rotating action of the furnace promotes better mixing and heat distribution, ensuring uniform melting and processing of the materials. This results in improved product quality and reduced processing time.
Additionally, rotary melting furnaces offer precise temperature control, allowing operators to achieve the desired melting point for the materials being processed. This level of control is essential in industries where specific temperature requirements are necessary for successful melting and processing.
Furthermore, these furnaces are designed with safety features to ensure the protection of both operators and the environment. They are equipped with advanced control systems and safety mechanisms to prevent accidents and minimize the release of harmful emissions.
In conclusion, rotary melting furnaces are versatile equipment that offers numerous advantages in terms of material handling, heat transfer, temperature control, and safety. Their ability to handle various materials and provide efficient melting and processing makes them valuable tools in industries that rely on precise and reliable melting processes.
conclusion
In conclusion, rotary melting furnaces, also known as rotary kilns, offer numerous advantages in the melting process. These innovative furnaces, designed with a rotating drum, have revolutionized the metal casting industry by improving efficiency and reducing energy consumption. The advancements in modern rotary melting furnaces have significantly enhanced the metal casting industry, making them a crucial component in the melting processes of various industries. One of the main advantages of rotary melting furnaces is their ability to efficiently melt various materials. The rotating action of the furnace promotes better mixing and heat distribution, ensuring uniform melting and processing of the materials. This not only enhances the quality of the final product but also increases productivity and reduces production costs. Furthermore, innovations in modern rotary melting furnaces have led to significant improvements in efficiency and energy consumption. The advancements in insulation materials and burner technology have made these furnaces more energy-efficient, reducing the overall energy consumption in the melting process. This not only benefits the environment but also helps companies save on energy costs. Additionally, rotary melting furnaces have proven to be versatile equipment used in various industries for the melting and processing of different materials. Whether it's metals, minerals, or even waste materials, these furnaces have the capability to handle a wide range of materials. This versatility allows industries to adapt and diversify their melting processes, meeting the demands of different applications. In conclusion, the advancements in modern rotary melting furnaces have significantly enhanced the metal casting industry. These furnaces play a vital role in enhancing efficiency and productivity in the melting processes. Their ability to efficiently melt various materials, along with improvements in energy consumption and versatility, make them a valuable asset in various industries. As the demand for high-quality and cost-effective melting processes continues to rise, rotary melting furnaces will undoubtedly continue to play a crucial role in meeting these demands.